I got some comments recently from bot, who suspected that the middle main cap deforming while ARP nuts were tightened could be the reason behind my seized crank.
The possibility of twisted or tweaked middle main cap didnt cross my mind. I had already gotten my block back from machine shop, when bot commented this thing, but I didnt have spare time to actually look my block until now.
I spent two hours carefully taking everything apart and examining the parts (once again). Block still had some cutting oil + metal particle residue from the honing and it probably was also mixed with that ARP moly stuff that was used on the threads. It took some time to get everything clean.
Below: I made a set of cylinder plugs from foam plastic to help with cleaning and installing parts.
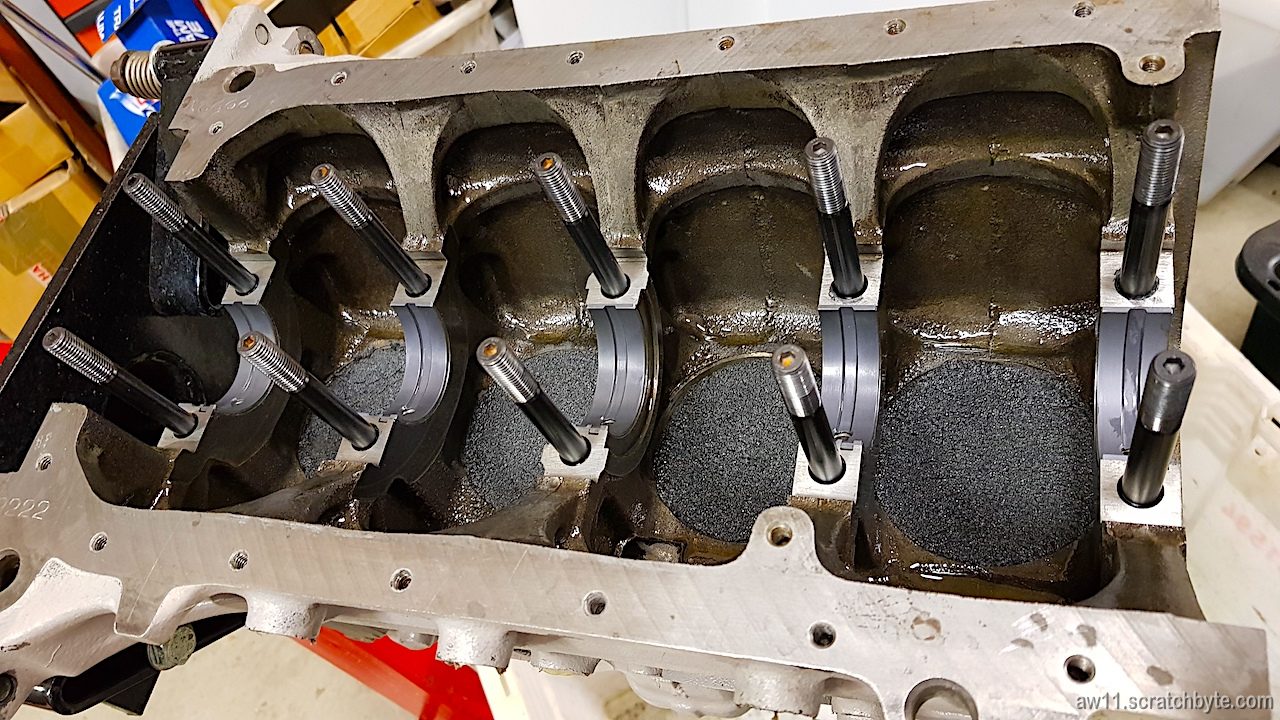
Putting everything back together went well. Bearings and ARP studs went in smoothly and so did the crank (after cleaning it millionth time). When I got to the thrust bearings I eyeballed them with suspicion but they didnt reveal anything to me. Lower ones slid in easily and the upper ones went in with the main cap.
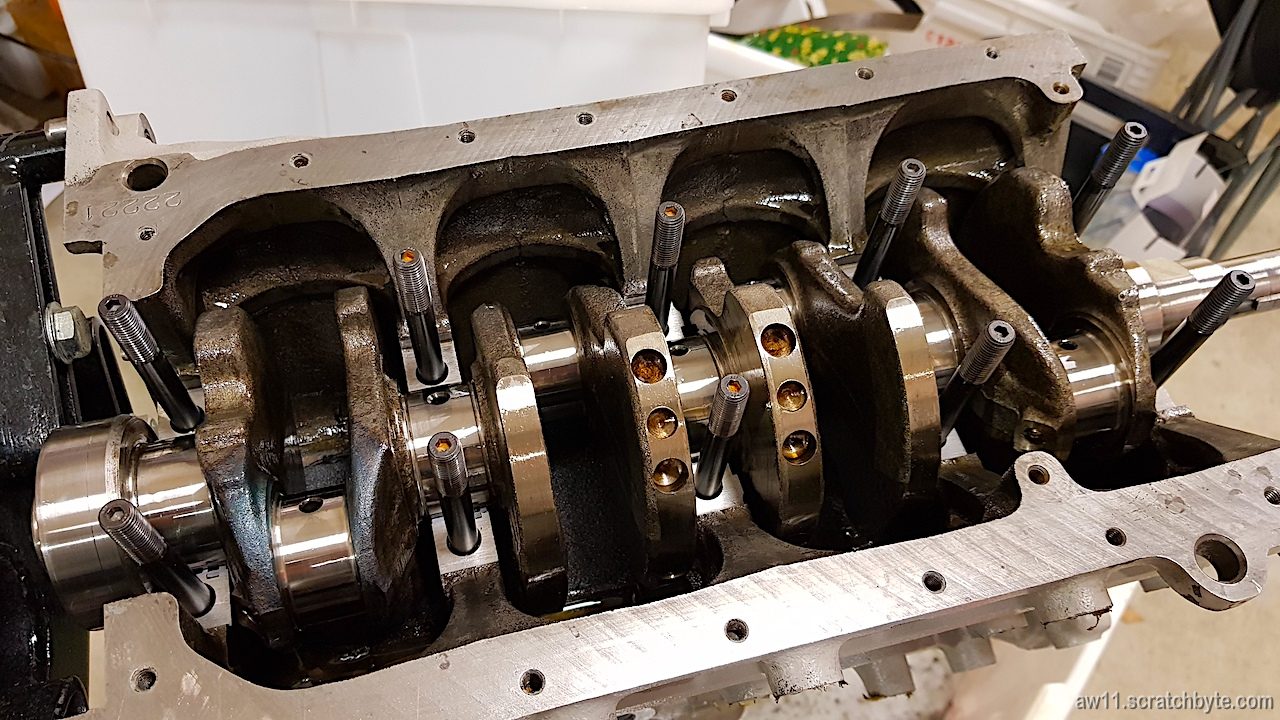
Last bits were the MRP girdle and ARP washers and nuts. I tightened the nuts in four steps starting from 20Nm and ending to 80Nm, stopping in between to rotate the crank and see if there were any problems. The crank rotated freely every time.
Below is my torque wrench. I bought this one just for this project to get the critical parts correctly torqued.
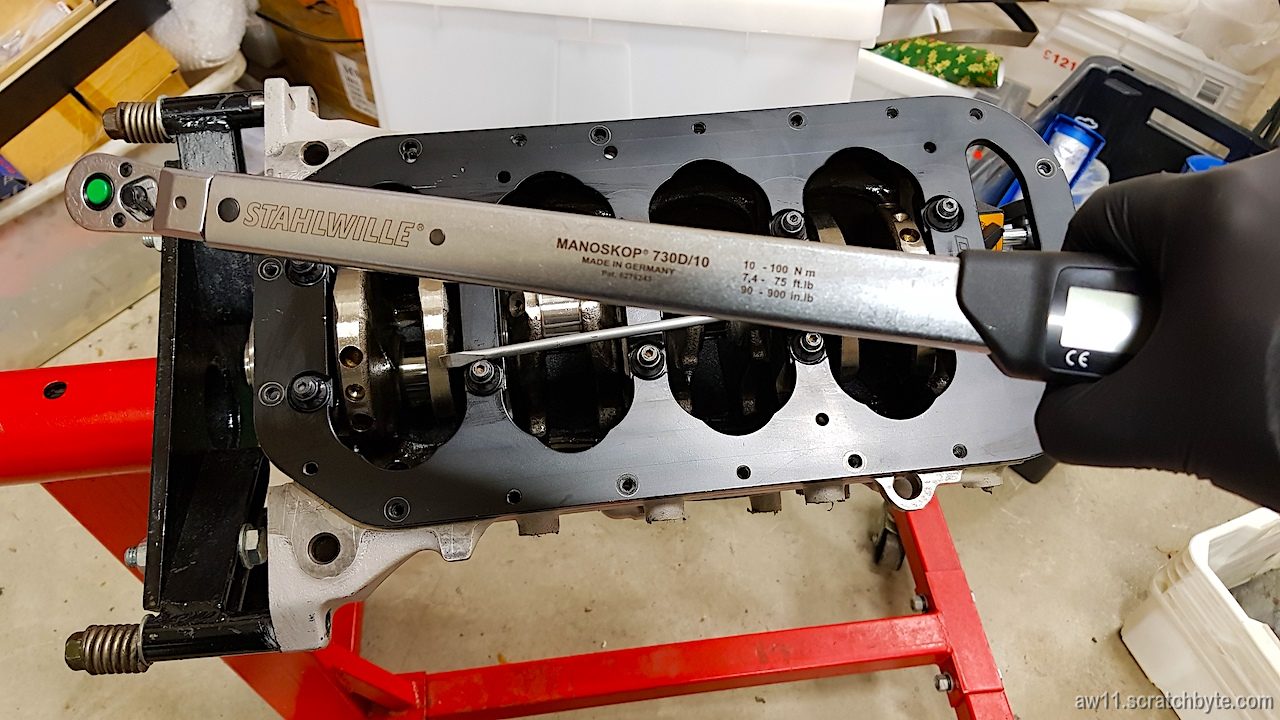
It started to seem that the honing did help and the middle cap wasnt causing any trouble. I grabbed the crank from the both ends and tried to shake it, but it felt like there wasnt any play. I went to get Widrics almost unused dial indicator and set it up.
Below: zeroed
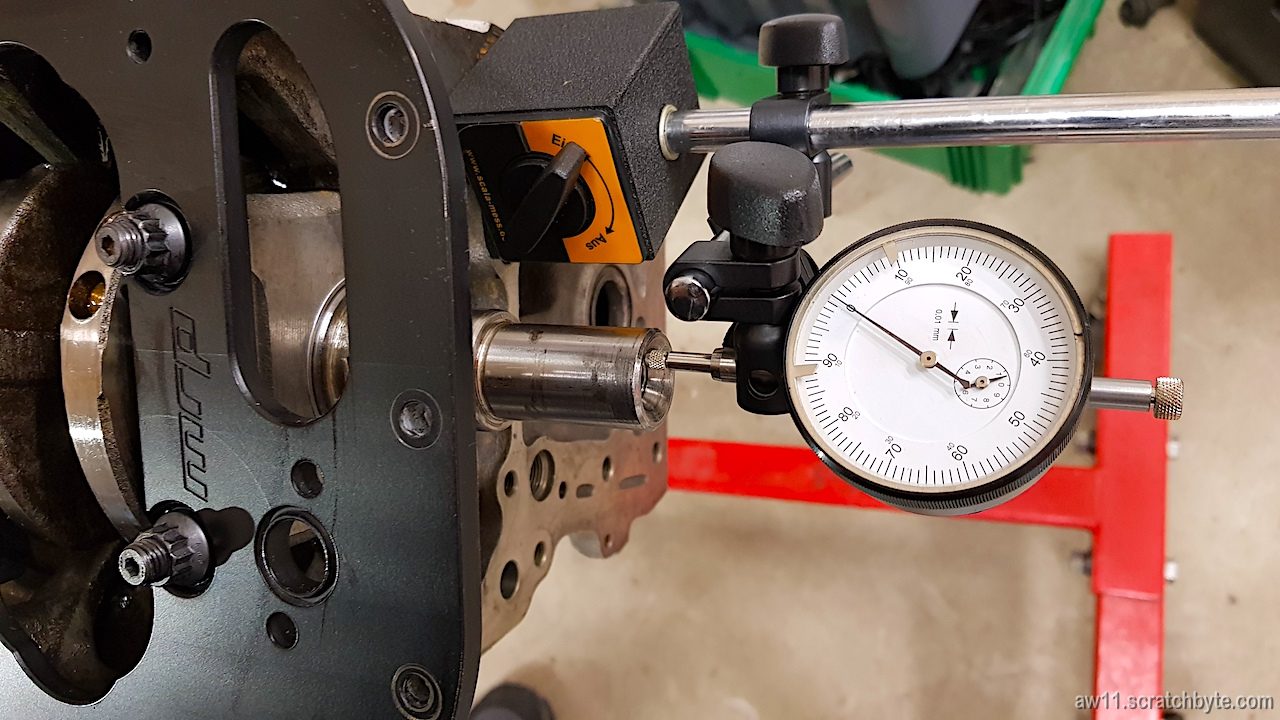
Then I poked the crank with screwdriver like the Toyota manual says.
Result: seems that my crankshaft end play is 0.03mm. Toyota manual says that the minimum acceptable is 0.02mm 😀
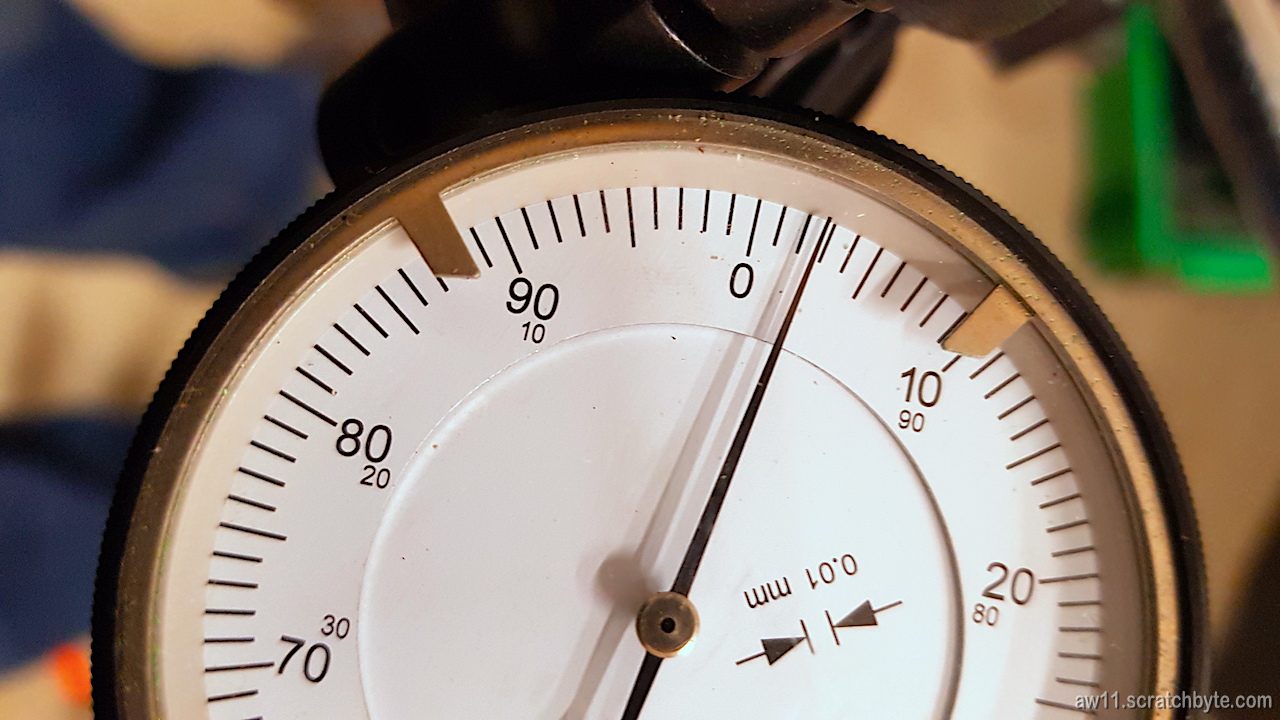
Some thoughts:
I’ve introduced plenty of new parts to my engine block. I have new main bearings and new thrust bearings, both with extra moly coating on them. Also, a set of longer ARP studs (with washers and nuts) for the girdle and the girdle itself.
Every new part creates a huge number of unknowns and it is absolutely important to check that everything is where they should be. Mr. Manon probably disagrees with me, but even the girdle could have been the source for my problems, although it got complemented by the machinist doing the honing 😀
Just by fitting all the parts together I found out that the middle main cap was not the problem. I’m not entirely happy of this method, but it has to do now. I dont have the resources and possibilities of McLaren to build engines 😀
Edit: My preferred method for the problem would have been different. I prefer to measure things until I have numbers, results and hard evidence. Except putting things back together was more practical and efficient method… 😀
I didnt measure the bearings yet, so next time I’ll be messing with plastigage.
and _o/ to bot!
Leave a Reply